Poor warehouse lighting makes everything harder—lower productivity, higher energy costs, and more safety hazards. And when the wrong lights go up, redoing it costs even more. Here’s how to do it right the first time.
LED warehouse lighting brings massive advantages—up to 70% energy savings, longer lifespan, better visibility, and improved safety. High bay and low bay LEDs cater to different ceiling heights, while vapor tight lights suit harsh environments. Proper lighting layout and beam spread matter just as much as fixture choice. With flexible control options and future-proofing, LED solutions adapt easily to warehouse changes, all while reducing maintenance and power costs.
Let’s dive in and figure out exactly what you need.
Table of Contents
Benefits of LED Warehouse Lighting
Switching to LED lights in a warehouse setting isn’t just trendy—it’s a game-changer. First, you cut down on power bills. LED high bay lights use up to 70% less energy than traditional metal halide or fluorescent fixtures. That means big savings, especially in large warehouses that run lighting for 12–24 hours a day.
Second, LEDs last longer—often 50,000 hours or more. That reduces maintenance downtime and the hassle of constant replacements. Third, the light output is sharper, more uniform, and doesn’t flicker. It enhances visibility, cuts down on eye strain, and reduces accidents.
With options like motion sensors, dimming functions, and tunable white, warehouse LEDs also give you better control. And they come on instantly—no warm-up needed like the old-school metal halide lamps.
Types of Warehouse Lighting
Selecting the right lighting for a warehouse is crucial for visibility, safety, and energy efficiency. Different warehouse setups require different types of LED lights. Here are the main options:
High Bay LED Lights
These are designed for ceilings higher than 6 meters (20 feet). High bay lights deliver powerful, focused illumination from a distance, making them ideal for large, open warehouse spaces. They come in round (UFO style) or linear formats, and often include options for motion sensors and dimming.
Low Bay LED Lights
Best suited for ceilings between 3 to 6 meters (10 to 20 feet), low bay lights are used in smaller warehouses, packing areas, or storage rooms. They offer wider beam angles to cover more ground with softer lighting. Low bays help maintain uniform brightness without creating harsh glare.
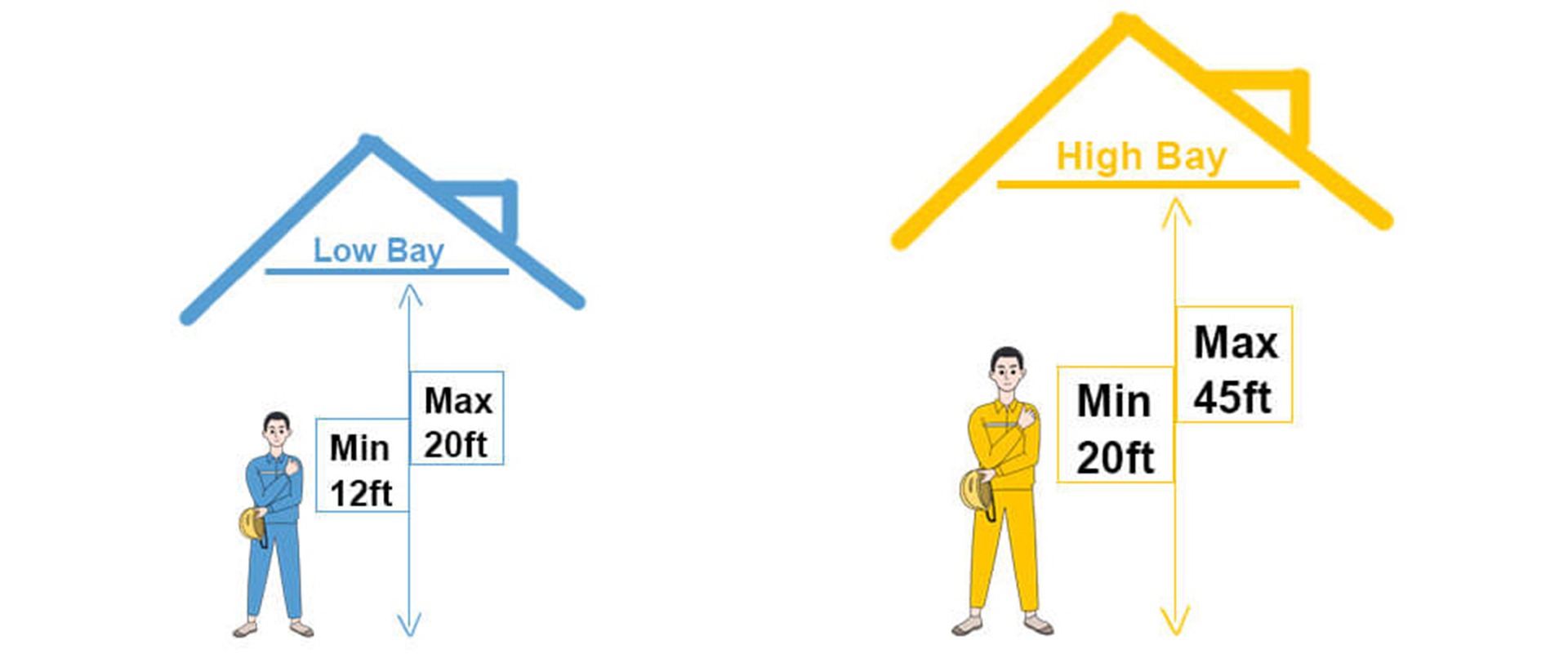
low bay vs high bay light
Linear LED High Bays
These fixtures are shaped like long fluorescent tubes but pack the punch of high-output LEDs. They’re perfect for aisles and shelving rows where lighting needs to run parallel to the layout. Linear high bays are common in logistics centers, fulfillment warehouses, and wholesale retail setups.
Vapor Tight LED Lights
Vapor tight lights are fully sealed against dust, moisture, and even chemical fumes. These are essential in warehouses where humidity, temperature swings, or wash-down conditions are common—like food storage, cold rooms, or industrial processing areas. The housing protects both the LEDs and the internal wiring from corrosion or damage.
Each lighting type serves a specific purpose. Choosing the right one depends on ceiling height, task zones, environmental conditions, and energy-saving goals.
Designing Warehouse Lighting Layouts
Lighting layout is everything. Even if you buy the best LED high bay light 200W on the market, if it’s installed in the wrong spot, your space will still look like a cave.
When designing a layout, consider:
- Ceiling Height: Higher ceilings need more powerful lights (and tighter beam angles).
- Mounting Height vs Light Spread: Make sure the beam reaches the floor evenly without creating dark zones.
- Lux Requirements: Warehouses typically need 100–300 lux depending on the work area.
- Rack Shadows: If your warehouse has shelving or racks, light should be placed to prevent shadows between rows.
- Spacing: Use lighting software or guidelines to calculate the distance between fixtures to maintain uniform light.
Want help designing yours? That’s what we do every day
Key Considerations Before Choosing Warehouse Lighting
1. Brightness and Light Levels
The amount of light needed in a warehouse depends on the tasks being done. General storage areas might need only 15–20 footcandles (or 150–200 lux), but areas where workers handle small parts or perform detailed tasks may need 30–50 footcandles (or 300–500 lux). Proper brightness ensures safety, reduces eye strain, and boosts productivity. Always refer to lighting standards such as OSHA or IES to guide your planning.
2. Space Layout and Ceiling Height
Your ceiling height and space configuration determine what type of fixture works best. High bay lights are designed for tall ceilings (typically 6 meters or higher), offering narrow beam angles to project light down to the floor. For lower ceilings, you might need strip lights or troffers that provide a broader spread. Consider rack heights and aisle spacing when placing fixtures for even coverage.
3. Operational Requirements and Zones
Different zones within the same warehouse may require different lighting setups. Loading docks need brighter, focused lighting, while storage areas may get by with moderate levels. Office areas might need softer, more comfortable light. Define lighting needs based on specific tasks and foot traffic in each section.
4. Color Temperature and Color Rendering
Color temperature impacts how workers perceive their environment. Cooler temperatures (5000K–6500K) provide crisp, white light that helps with focus and detail-oriented tasks. Warmer tones (3000K–4000K) are better for break rooms or office spaces. High CRI (Color Rendering Index) ensures accurate color visibility, useful for sorting, labeling, and quality inspection.
5. Energy Efficiency and Cost Savings
LED warehouse lights are known for using up to 75% less energy than traditional options like metal halide or fluorescent. Choosing high-lumen-per-watt fixtures helps you get more light with less power. Over time, this reduces your electric bill and total cost of ownership.
6. Safety and Compliance
Well-lit warehouses reduce the risk of accidents, especially in aisles, stairwells, or loading zones. Lighting should meet local safety codes and workplace standards. Emergency lighting and clearly marked escape routes should also be part of your lighting plan to comply with fire and safety regulations.
7. Flexibility and Future-Proofing
Your warehouse might change—new shelving, new equipment, or expanded operations. Choose lighting that’s easy to move, dim, or automate. Fixtures with motion sensors, daylight harvesting, or smart controls make it easier to adapt lighting as your space evolves.
8. Fixture Type and Beam Angle
Different fixtures serve different purposes. UFO high bays offer wide-area coverage, while linear high bays work well in narrow aisles. Beam angle affects how the light spreads: narrow beams focus light downward for higher ceilings, while wide beams spread light across broad spaces. Matching the right type and angle improves both efficiency and visual comfort.
9. Durability and Environmental Factors
Warehouse lights must endure dust, vibration, humidity, and temperature changes. Look for fixtures with IP ratings (like IP65 for moisture resistance) and strong housings. In food storage or industrial settings, vapor-tight fixtures or shatterproof lenses may be required to meet hygiene and safety rules.
Understanding these factors helps you build a warehouse lighting plan that saves money, keeps workers safe, and stays reliable over time.
Summary Table of Considerations
Consideration | Key Points |
---|---|
Brightness and Light Levels | 15–50 footcandles based on task; follow OSHA/IES guidelines |
Space Layout & Ceiling Height | Use high bays for tall ceilings; strips or troffers for lower ceilings |
Operational Zones | Adjust lighting per zone—e.g., docks need brighter lighting than storage |
Color Temp & Rendering | 5000K–6500K for clarity; 3000K–4000K for comfort; CRI 80+ for accuracy |
Energy Efficiency | LEDs cut energy use up to 75%; higher lumens per watt = better savings |
Safety and Compliance | Meets safety codes; improves visibility to prevent workplace accidents |
Flexibility & Future-Proofing | Sensor-ready, dimmable, and easily repositioned for changing layouts |
Fixture Type & Beam Angle | Match fixture type and beam spread to space, task, and mounting height |
Durability & Environment | Use IP-rated, vibration-resistant lights in tough industrial settings |
By evaluating these factors, warehouse managers can select lighting that improves productivity, boosts safety, and cuts costs while staying adaptable for future needs.
How Can You Tell if an LED Light Is Good Quality?
There are a few simple ways to spot a high-quality LED light. Start with the internal components. Reliable lights use well-known LED chips from brands like Lumileds, Osram, or Seoul. The driver is just as important—look for names like Philips, Mean Well, or Inventronics. These parts directly affect the light’s performance and lifespan.
Next, check the warranty. A solid 5-year warranty is a good sign the manufacturer trusts their product. Also, look for international safety certifications like CE, RoHS, UL, or DLC. These show that the product meets certain quality and safety standards.
Physically, a good LED light should feel sturdy. It will likely have an aluminum or metal housing, not plastic. This helps with heat dissipation, which keeps the internal components from overheating and extends the fixture’s life. For outdoor or industrial use, make sure it has a waterproof rating of at least IP65. That means it can resist dust and heavy rain.
In short, you can tell an LED light is good quality by the brand of its chip and driver, the build materials, the warranty, and the certifications it carries.
FAQs About Warehouse Lighting
How many lumens do I need for a warehouse light?
It depends on your ceiling height and space size. For high bay fixtures in a typical warehouse, 20,000–30,000 lumens is ideal. Use higher lumen lights for spaces above 10 meters in height.
How do you calculate how many lights you need for a warehouse?
First, measure your area in square meters. Then decide on your required lux level (usually 100–300 lux). Use the formula: Total Lumens Needed = Area × Lux Level. Then divide by the lumen output of your chosen fixture.
How do I know what LED lights to buy?
Start with ceiling height, usage (storage vs work), and area size. Then check lumen output, beam angle, and mounting type. Always ask for product datasheets and photometric diagrams.
Conclusion
Picking the right LED warehouse lighting isn’t just about brightness—it’s about making your workspace safer, more productive, and more cost-effective. With so many options on the market, taking time to plan your layout and choose quality fixtures makes all the difference.
Got a project or need advice? Feel free to reach out to us directly. Let’s light your warehouse the right way.
Request A Free Quote Now!
Send us a message if you have any questions or request a quote. We will get back to you ASAP!